Traditional surface cleaning methods—like chemical stripping, abrasive blasting, and wet sanding—have been used for years to remove rust, paint removal, and removing contaminants. But these methods come with serious problems. They can damage the substrate, create toxic waste, and pose health risks to workers. Thankfully, there’s a better way: laser blasting. This modern laser cleaning process is eco-friendly, cost-effective, and highly efficient for clean surfaces in various industrial applications.
Why Traditional Cleaning Methods Are a Problem
Many industries still use traditional cleaning methods that rely on chemicals, high-pressure water, and abrasive materials to clean surfaces. These techniques may work, but they cause major issues:
- Chemical Stripping: Uses harsh solvents that produce toxic fumes and can damage the substrate.
- Abrasive Blasting (Sandblasting, Soda Blasting): Wears down delicate surfaces and spreads dust and debris.
- Wet Sanding & High-Pressure Cleaning: Requires a large amount of water, leading to environmental waste.
These methods aren’t just harmful—they’re also expensive, time-consuming, and difficult to control. They’re especially risky for stainless steel, industrial applications, and historic restoration projects, where damage is not an option.
How the Laser Cleaning Process Works
Industry laser technology uses short pulse bursts to perform laser ablation, which removes contaminants without damaging the substrate. This high-quality, non-contact process vaporizes unwanted materials, leaving the original surface clean and intact.
The Advantages of Laser Cleaning Systems
1. Environmentally Friendly & Waste-Free
Unlike traditional cleaning methods, laser cleaning machines do not use chemicals, water, or abrasive materials. This means:
- No hazardous waste to dispose of.
- No harmful fumes or toxic byproducts.
- A safer option for workers and the environment.
2. High-Quality Results Without Damage
The laser cleaning process only removes paint, rust, or contaminants, leaving the original material untouched. It’s perfect for:
- Historic restoration projects where delicate stone or wood must be preserved.
- Stainless steel and metal parts that need paint removal without weakening the structure.
- Industrial applications where precision surface cleaning is required.
3. Safer for Workers
Working with chemical paint removers, lead-based paint, and abrasive materials can expose workers to serious health risks. Laser ablation reduces exposure to:
- Lead dust from old painted surfaces.
- Toxic chemicals that require protective gear.
- Flying debris from sandblasting.
By keeping the work area cleaner and safer, laser cleaning machines lower the risk of inhalation injuries, burns, and long-term exposure effects.
4. A Cost-Effective Solution
While the initial investment in laser cleaning systems might be higher, it quickly pays for itself because:
- There are no consumables like sand, water, or chemicals.
- Minimal cleanup reduces labor costs.
- It extends the lifespan of materials by preventing unnecessary wear.
- Significant cost savings in the long run due to reduced maintenance.
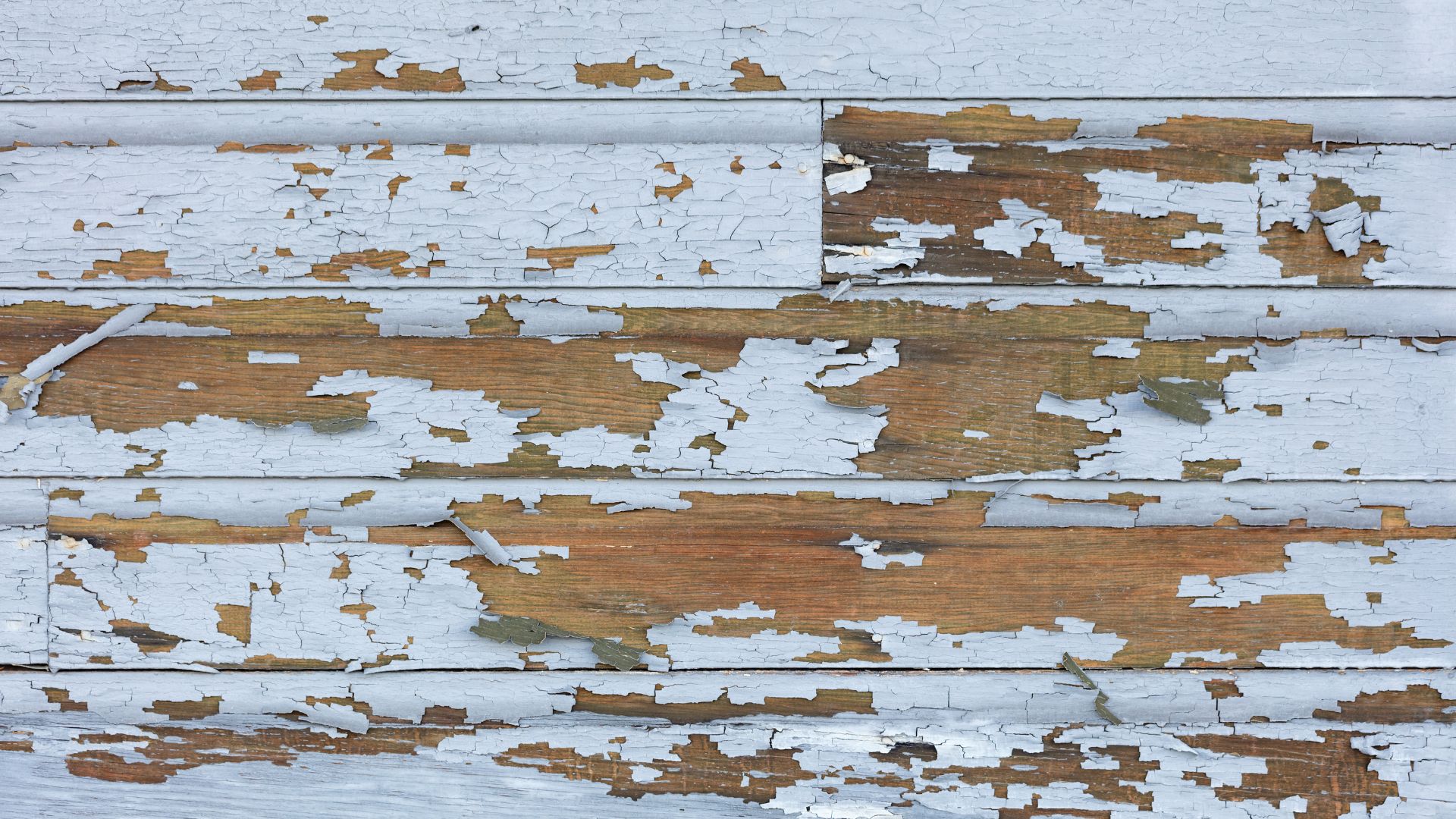
Who Can Benefit from Laser Cleaning Machines?
Laser cleaning systems are used across a wide range of industries, from restoration to manufacturing. Some of the most common users include:
- Historic Restoration Experts – Removing paint removal contaminants from heritage buildings without damaging the substrate.
- Aerospace & Automotive Industries – Stripping coatings from stainless steel and other metals.
- Manufacturers & Industrial Facilities – Cleaning tools and machinery without downtime.
- Construction & Property Managers – Removing graffiti, oxidation, and contaminants without high-pressure blasting.
Medical & Electronics Industries – Cleaning precision instruments where contamination control is critical.
Example: A Perfect Laser Cleaning Customer
Imagine a contractor restoring a 100-year-old government building. The building’s brick walls and wooden trim are coated in lead-based paint, which must be removed without damaging the substrate. Traditional cleaning methods—like wet sanding or chemical stripping—would create toxic waste and could wear away the delicate surface.
By using laser cleaning systems, the contractor can remove lead-based paint safely, without damaging the building. This method keeps the work area clean, prevents lead dust from spreading, and protects the structure for future generations.
Frequently Asked Questions (FAQ)
Does the laser cleaning process work on all surfaces?
Yes! Laser cleaning machines are safe for stone, wood, brick, concrete, stainless steel, and metal. It removes paint removal contaminants without causing damage.
Does laser ablation create lead dust?
No. Unlike sanding or blasting, laser ablation vaporizes lead-based coatings, reducing the risk of contamination.
Is laser cleaning a cost-effective solution?
Yes! While the upfront cost is higher, cost savings come from eliminating waste disposal, reducing cleanup, and preventing surface damage.
How long does it take to clean a surface?
It depends on the size and material, but laser cleaning machines work faster than traditional cleaning methods since there’s no prep or cleanup.
Can I use a laser cleaning system for home projects?
Yes! If you have paint in your home that contains lead or other contaminants, laser cleaning systems are a safe, effective way to remove it without toxic chemicals.
Laser Cleaning in Calgary | ZAP
At ZAP Laser Cleaning, we specialize in eco-friendly, safe, and effective surface cleaning. Our laser cleaning machines remove rust, paint removal, oxidation, and contaminants from a wide range of surfaces, including historic sites, industrial equipment, and older homes.
Say goodbye to harsh chemicals, expensive maintenance, and hours of cleanup.
Contact ZAP Laser Cleaning today to learn how our industry laser technology can revolutionize your restoration project!